
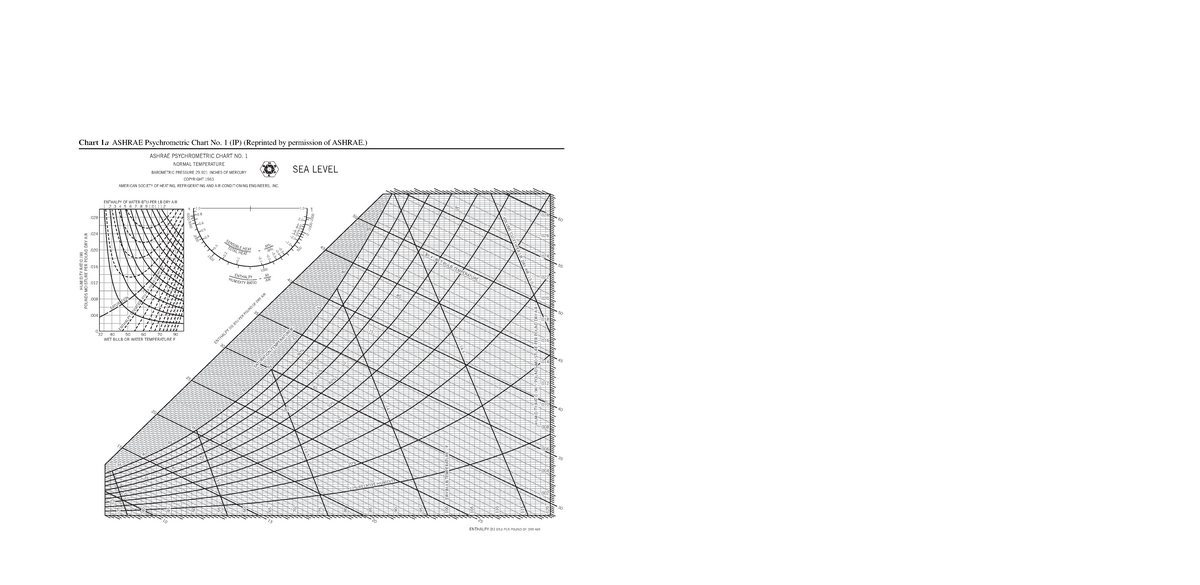
Select “Auto” initialization so that the initial parameters are calculated by the software.
#ASHRAE PSYCHROMETRIC CHART NO 2 SOFTWARE#
There are however many measures that can be taken to fix the problem from the software input windows. Numerical instability during the program run is unfortunately a problem with most software packages of this nature. The software appears to be not running if the solution algorithm becomes numerically unstable. The only problem is that there are only a few facilities globally where tests like these can be conducted.

This can be a costly undertaking, but if you take the penalties involved if a cooling tower does not meet the guaranteed performance, this is a small price to pay. The only way to be certain of what the transfer characteristics are for a fill, is to do an independent fill test. If you are aware of any other sources that give fill performance data, then I would appreciate it if you can let me know about it. (ed.), Cooling Tower Performance Prediction and Improvement, Volume 1, Applications Guide, EPRI Report GS-6370, Volume 2, Knowledge Base, EPRI Report GS-6370, EPRI, Palo Alto, 1989. and Christie, D.G., Heat Transfer and Pressure Drop Data on Cooling Tower Packings and Model Studies of the Resistance of Natural Draft Towers to Airflow, Proceedings of the International Heat Transfer Conference, Colorado, Part V, pp. The following two sources do give transfer coefficients of various fills: One of the reasons for this is that fill manufacturer’s regard the transfer characteristics of their fills as confidential. Unlike heat exchangers, where transfer coefficients for various configurations are widely published, cooling tower transfer characteristics are not commonly found in the open literature.
#ASHRAE PSYCHROMETRIC CHART NO 2 HOW TO#
Refer to the second point in the blog entry entitled “Fan Specification” on how to do this.Ĭooling tower transfer characteristics is one of the most, if not the most important parameters in cooling tower thermal design. When the tower design is complete a fan must be selected. A decision can now be made to l alter the air flow rate, the fill height or both. With the first run of the software the water outlet temperature will probably be too hot or too cold. A trail and error process will now be conducted to achieve the design water outlet temperature. The rest of the inputs in the software should be typical for mechanical draft cooling towers. the air flow rate is equal to the water mass flow rate. A Gw/Ga ratio of one is therefore a good first assumption, i.e. According to one publication the ratio of the water and air flow mass velocities (Gw/Ga) should be between 0.75 and 1.5 for mechanical draft cooling towers. A first guess for the air flow rate is based on the following. The next decision is the required air flow rate. Pick any number of layers that will give a practical height, e.g. Assuming a square tower the actual inside dimensions of the tower can now be determined.Ĭooling tower fills are generally packed in layers where the layers have a fixed height. Lets assume for argument sake that the actual plan area is 1.05 times the area of the fill. The actual area of the cooling tower is larger than the area of the fill due to the area that the fill supports etc.

It is further assumed that the tower is square. If the recommended Gw for the fill is known Afr can now be calculated, where Afr = mwi/Gw Your fill supplier should be able to tell you what the typical recommended range for Gw is.
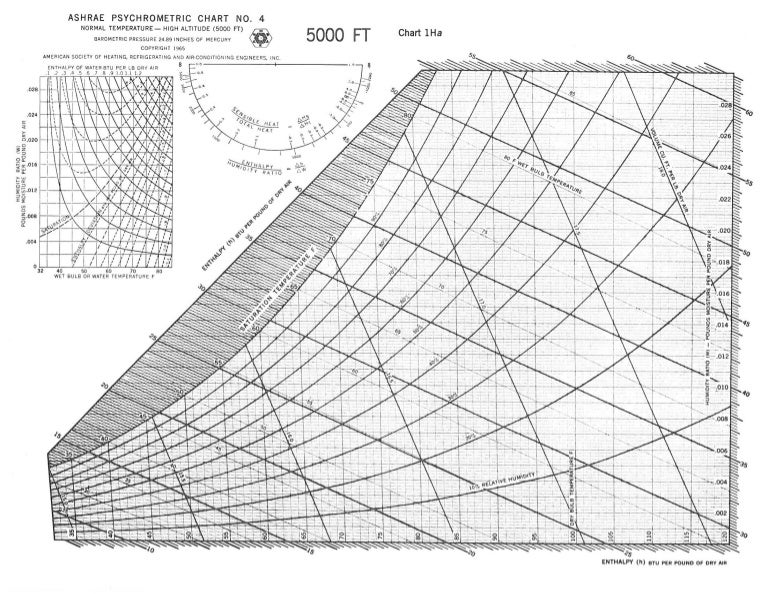
One parameter that can guide you in this decision is the water mass velocity, Gw, where Gw = mwi/Afr. The first important design decision one needs to make is what the frontal area of the fill (Afr) should be. The decision of the type of fill will be a function of the water quality and the fouling propensity of the fill. It is also advisable at this stage to know what type of fill will be employed. The process typically involves some trial-and-error to obtain the desired water outlet temperature.įor a start the following design conditions must be specified: The software is then employed to optimize the design. The steps below should give an appropriate starting point for the design process with my cooling tower software. Where does one start when designing a mechanical draft cooling tower from scratch? This can be quite a daunting task as there are many variables and opposing objectives when optimizing the design.
